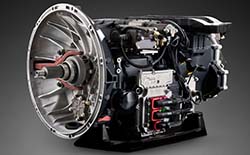
Scania Achieves Milestone in Sustainable Manufacturing with Remanufactured Gearboxes
Posted: 03-Oct-2024 |
In a groundbreaking move for the heavy vehicle industry, Scania has become the world's first truck Original Equipment Manufacturer (OEM) to incorporate reused components directly into its main assembly line. This historic achievement marks a significant step towards sustainable manufacturing practices and a circular economy.
The milestone was reached earlier this year as part of the innovative iReGear joint research project, developed in collaboration with KTH Royal Institute of Technology and Scandinavian Transmission Service AB. Funded by Vinnova, the Swedish innovation agency, the project focused on the remanufacturing of gearboxes, which demonstrated substantial environmental benefits.
The remanufactured gearbox, subjected to rigorous quality and functionality tests equivalent to its new counterparts, resulted in approximately 50 percent less material consumption and generated 45 percent fewer carbon emissions than conventional manufacturing processes. The gearbox underwent testing on the same sophisticated rigs as new gearboxes, with approximately 100 quality and function parameters monitored to ensure it met Scania's high performance and quality standards.
"As good as new," the remanufactured gearbox stands as a testament to the feasibility of integrating reused components into new vehicle production, challenging the industry norm that has largely relegated remanufactured parts to the aftermarket sector. According to a 2015 report by the European Remanufacturing Network, remanufactured parts account for only 1.1 percent of new manufacturing in the European automotive sector.
The iReGear project underscores the potential of remanufacturing as a strategy to address resource scarcity and achieve climate goals in the automotive industry. By rethinking the role of remanufactured components, Scania aims to inspire other vehicle manufacturers to follow suit, paving the way for a more sustainable transport industry.
“What an achievement by the project and everyone involved. This remanufactured gearbox is a compelling example of how the manufacturing of heavy vehicles can become more sustainable, circular, and efficient while still retaining the highest quality standards,” said Fredrik Nilzén, Head of Sustainability at Scania.
Farazee Asif, an Assistant Professor at KTH, noted, “This research provides the first evidence to support the argument that it is feasible to envision future manufacturing organisations seamlessly integrating manufacturing and remanufacturing operations to develop Circular Manufacturing Systems that consume fewer resources, produce fewer emissions, and cost less without compromising quality and performance.”
Ola Stålebo, CEO of Scandinavian Transmission Service AB, echoed the significance of this advancement, stating, “STS has been remanufacturing gearboxes for more than 50 years. It’s amazing to be able to challenge the old perception that remanufactured parts can only be used for aftermarket purposes. Today, we can proudly reflect on a period of successful collaboration, where we have achieved breakthroughs in sustainable technology. This project truly shows that it might not need to stop at just one idea, but it could become a reality in the near future.”
Scania’s pioneering efforts pave the way for a paradigm shift in the manufacturing practices of heavy vehicles, emphasising sustainability and resource efficiency without sacrificing performance or quality. As the industry navigates increasing environmental challenges, initiatives like the iReGear project represent vital steps toward a greener, more circular economy.