Aeolus Truck & Driver News

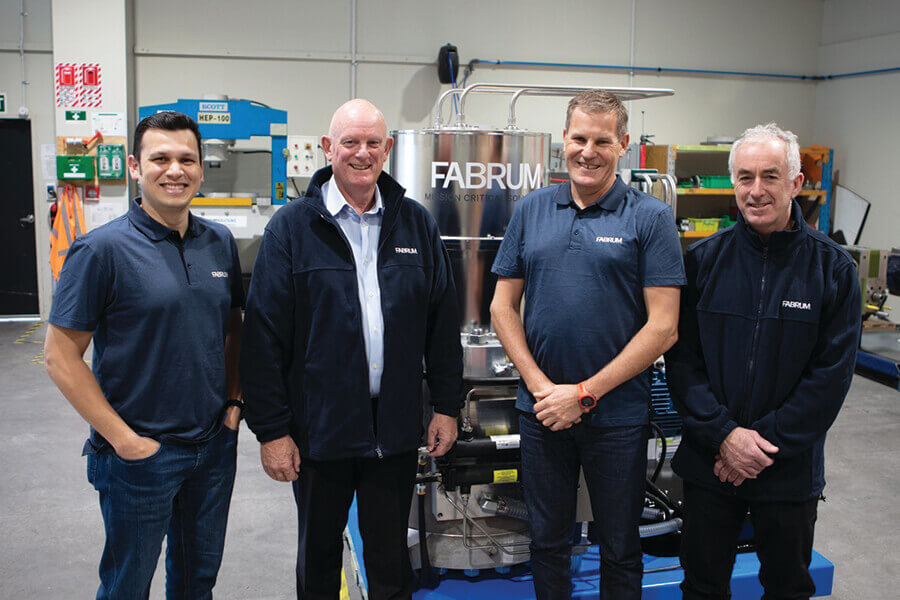
Kiwi tech drives dual-fuel truck trial
Aeolus Truck & Driver News
A Christchurch company with expertise in a wide range of advanced technology worldwide is a key collaborator in the HWR Group’s trial of dual-fuel diesel/hydrogen trucks.
Tucked away in the industrial suburb of Hornby, Fabrum is a leading producer of the cryogenic systems used to liquefy a range of gases – including nitrogen, oxygen, air and even hydrogen – and has used this expertise to develop what CEO Ojas Mahapatra calls an “end-to-end system to deliver hydrogen for transport fuel applications.”
Fabrum has been around for some 18 years, its core intellectual property being focused on cryogenic cooling and the composite materials used to fashion storage containers for the liquid gases. The practical applications cover a huge range – from animal husbandry (using liquid nitrogen to freeze bull semen) through the development of high-powered magnets and electric motors that depend on superconducting materials, to aerospace projects.
Among the more high-profile of these was the development of a CO2 sublimation system for NASA’s Mars lander’s future flight, while no less high-profile (if closer to Earth) is Emirates Team New Zealand’s recently launched foiling chase boat, powered by hydrogen fuel cells supplied by Toyota and with its onboard hydrogen storage courtesy of Fabrum.
...A Christchurch company with expertise in a wide range of advanced technology worldwide is a key collaborator in the HWR Group’s trial of dual-fuel diesel/hydrogen trucks.
Tucked away in the industrial suburb of Hornby, Fabrum is a leading producer of the cryogenic systems used to liquefy a range of gases – including nitrogen, oxygen, air and even hydrogen – and has used this expertise to develop what CEO Ojas Mahapatra calls an “end-to-end system to deliver hydrogen for transport fuel applications.”
Fabrum has been around for some 18 years, its core intellectual property being focused on cryogenic cooling and the composite materials used to fashion storage containers for the liquid gases. The practical applications cover a huge range – from animal husbandry (using liquid nitrogen to freeze bull semen) through the development of high-powered magnets and electric motors that depend on superconducting materials, to aerospace projects.
Among the more high-profile of these was the development of a CO2 sublimation system for NASA’s Mars lander’s future flight, while no less high-profile (if closer to Earth) is Emirates Team New Zealand’s recently launched foiling chase boat, powered by hydrogen fuel cells supplied by Toyota and with its onboard hydrogen storage courtesy of Fabrum.
In between these extremes is a collaboration with Magnix, a leader in the development of superconducting electric motors for commercial aircraft.
Fabrum was set up in 2004 by two engineering graduates from the University of Canterbury, Chris Boyle and Hugh Reynolds, with the aim of developing the cryogenic systems and associated composite-material storage needed for advanced
superconducting materials, which call for very low operating temperatures.
Over the years Fabrum has become one of the world’s leading builders and suppliers of industrial cryocoolers. Key characteristics of these is their robustness and a standardised, modular design that makes them a virtually ‘plug and play’ proposition and allows multiple modules to be stacked for greater output.
The growing importance of hydrogen as a replacement for fossil fuels in transport fits neatly with Fabrum’s expertise, explains Ojas Mahapatra: “When the concept of a hydrogen ecosystem began to attract attention, it was simple to take our intellectual property and apply it.
“Recently we partnered with UK company CPH2 to integrate our cryocoolers with their membrane-free electrolysers to separate the co-mingled hydrogen/oxygen gas stream into its constituent parts. Oxygen becomes liquid at -183degC, while for hydrogen the point is lower again, -253degC. That means the two gases are completely separated, and also very pure.”
CPH2 electrolysers are at the heart of the HWR Group dual-fuel truck trial. They are based on a patented membrane-free design, unlike more conventional PEM (proton exchange membrane) designs which use a thin polymer membrane between the anode and cathode that allows the passage of positive hydrogen ions but blocks the oxygen ions that are the other product of splitting the water. The result is separate streams of each gas from the opposite sides of the cell.
By comparison, the CPH2 design produces the gases between the plates and co-mingled, calling for their cryogenic separation as described above.
Its benefits, says CPH2, include dispensing with the rare-earth catalysts (platinum, palladium or iridium) required by PEM designs and a far longer economic life, up to 25 years versus five.
CPH2’s MFE220 electrolyser can produce up to 450kg of hydrogen per day. At the 60/40 diesel/hydrogen mix that seems the sweet spot for keeping NOx outputs in check, this output would be sufficient to look after 11-12 typical heavy trucks, each covering 600km a day.
Fabrum is uniquely placed to offer a complete package for the transport industry as it transitions away from fossil fuels, says Mahapatra.
“As part of the complete hydrogen answer we also build the composite-material storage tanks and have also developed the dispenser technology for vehicle and aircraft refuelling.
“Shifting to green energy makes sense, which is why there is a big push in that direction. For the heavy vehicle industry, the transitional phase offered by hydrogen dual-fuel means that trucks can continue to operate over their full economic life. Their replacements could well be full hydrogen, but in the meantime the existing fleets can run with minor modification yet offer a significant reduction in fossil fuel use and carbon output.
“Industrial-level production, storage and transport of hydrogen presents significant challenges, challenges that are reduced markedly by the modular electrolysis systems that are the foundation of the HWR project. It is much easier to make and use it on the spot. HWR are in a perfect position to influence change. They have their own fleet, but, via Allied Petroleum they also have the infrastructure to sell the hydrogen to other users.
“There is a widespread sense that mainstream hydrogen applications for transport are maybe 5-10 years out – but in fact they’re here now.”