Southpac Legends
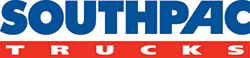
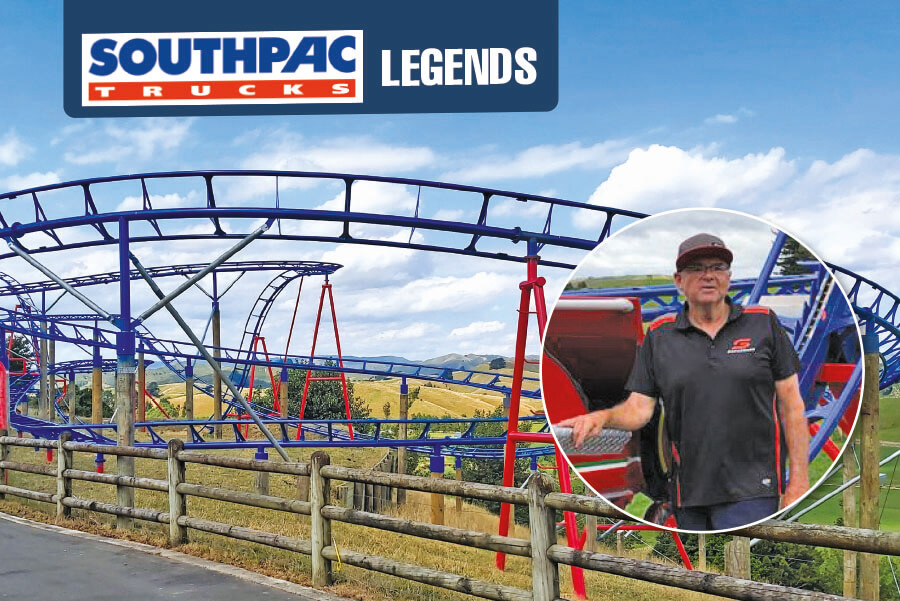
Trevor Jackson
Southpac Legends
To say Trevor Jackson has had a rollercoaster ride in life wouldn’t be strictly true. Like any company, his Pahiatua-based trailer maker, Jackson Enterprises, has had its share of ups and downs, but overall it has built an enviable reputation for innovation and quality and has enjoyed steady growth.
In a literal sense, though, Trevor’s life is a rollercoaster – courtesy of a full-size, 380m track he has designed and built on his rural property. The project took three and a half years to complete and had its maiden run just a few months ago, on New Year’s Eve 2021. Trevor was the guinea pig for the inaugural ride and recalls the sensation: “I strapped myself into the four-seater car and off we went. I nearly shit myself!”
Apart from the occasional shutdown for modification and tinkering, the track has run regularly ever since.
Inspiration for the project, he says, came from his three daughters, and he is looking forward to his grandchildren enjoying it for many years to come.
...To say Trevor Jackson has had a rollercoaster ride in life wouldn’t be strictly true. Like any company, his Pahiatua-based trailer maker, Jackson Enterprises, has had its share of ups and downs, but overall it has built an enviable reputation for innovation and quality and has enjoyed steady growth.
In a literal sense, though, Trevor’s life is a rollercoaster – courtesy of a full-size, 380m track he has designed and built on his rural property. The project took three and a half years to complete and had its maiden run just a few months ago, on New Year’s Eve 2021. Trevor was the guinea pig for the inaugural ride and recalls the sensation: “I strapped myself into the four-seater car and off we went. I nearly shit myself!”
Apart from the occasional shutdown for modification and tinkering, the track has run regularly ever since.
Inspiration for the project, he says, came from his three daughters, and he is looking forward to his grandchildren enjoying it for many years to come.
Construction was not a problem, he adds: “We have a talented team here who are dealing with steel welding all the time. Nor was getting approval from the local council too much of a hassle. In fact, the biggest challenge was that the shed housing the drive mechanism was a couple of square metres over regulations and it took a while to get a special permit for that. There was also a height restriction of 10 metres, but we needed something over 13 metres to gain the momentum to do the full distance... so we just dug a trench and put the structure into that!”
The 31-year history of Jackson Enterprises is peppered with dozens of examples of thinking outside the square. Among the ones that stand out in Trevor’s mind are the roll-up curtains for the export Gib-board trailers operated by Auckland’s CV Compton Ltd for Winstones. The trailers were built to a special over-width permit, at 2650mm, to ensure the 2400mm-wide sheets of Gib could be carted to port without damage to their edges. The permit specified that the trailer units could only be used on that project.
The curtains were fitted to drums, ensuring an optimal saving in width. The design was also dictated by regulations at the production facility that the truck drivers had to remain in their cabs.
Another interesting and challenging project he recalls was the transporter developed for Solid Energy at the Stockton mine on the South Island’s West Coast. The unit featured five rows of two axles, with four wheels per axle. The trailer itself weighed 57t, and it was capable of carrying 200t excavators. The tractor unit was based on a CAT 777 off-road dump truck, its 12-cylinder C32 engine producing just over 1000hp.
Another Jackson Enterprises specialty has been the company’s remotely operated effluent valves, developed in the late 1990s and fitted to stock crates. The valves are a standard fitment on all Jackson stock trailers and have gained a solid reputation in Australia, where they are used by four of that country’s stock trailer makers.
Jackson Enterprises’ base has always been in Pahiatua, though, as Trevor explains, in its early days the company wasn’t a trailer manufacturer but a servicing and repair operation for the local transport industry. “We did a bit of everything, and the trailer building grew from clients asking if we could provide them with some gear. This was about six years into the operation.”
The company’s birth was a pretty good indicator of the unconventional way of doing things that would become its hallmark, Trevor explains: “The first buildings we had were bought from the Ministry of Works at Turangi. They had been built to service the tunnelling operations for the Tongariro power scheme during the 1960s and ‘70s and housed repair depots and parts stores and the like. I bought them at auction for $19,000. A team of us then went up to Turangi and over the next couple of weeks we disassembled them, stacked them on trucks and trailers and drove them back to Pahiatua.
“The structures were steel frames with corrugated iron cladding. By the time we had broken them down and stacked them they didn’t bulk up all that much, going no higher than the sides on a conventional truck, but they were heavy. We had two units – both three-axle trucks and four-axle trailers – and they came back home at around 45 tonnes each! That was in the days of 38t maximum. We had no idea they were so heavy.
“An interesting thing about the structures was that, though there was provision for bolts, all the purlins and cleats in the roof were held to the main frame by wire.
“The deal involved three long buildings in a row. I kept the third of one of them and sold the balance off to pay for the land that we are still on.”
Within a couple of years beginning to build trailers, Trevor introduced a couple of innovations that have become Jackson Enterprises’ effective trademark – monocoque construction that integrates chassis and body, and the use of aluminium. He explains that the move was prompted by a desire to reduce tare weight, that benefit accruing mainly from the monocoque design rather than the material: “If a design calls for a particular thickness of steel, then you need double that thickness of aluminium. Of course, with trailers getting bigger all the time, the weight saving from monocoque is improving as well.”
The company produces all its designs in both aluminium and steel. Traditionally the balance has been around half and half, but in the past couple of years it has started to shift in favour of aluminium. As Trevor points out, it’s impossible to tell from a glance at a trailer on the road which material is used.
He is most proud of the finish of the company’s products: “That has been our primary goal from the very start. Design innovation and reliability are critical, of course, but given that all makers are producing quality products the key difference now lies in the finish and presentation.
“We have had instances of experienced drivers who are new to a fleet saying they want our gear when a new truck is being specced. We have picked up new customers that way.”
Jackson’s provides trailers for the country’s three stock crate makers, Delta, Total and Nationwide. In conjunction with the trio, it has developed a standardised trailer design that accommodates their varying designs, for significant cost savings. A similar outcome has been achieved after negotiation with the makers of car transporter bodies.
Apart from the rollercoaster, Trevor’s other major hobby project has been a 1959 Chev Corvette, imported from the USA and painstakingly restored over 12 years. The car runs the 283 cu in small-block V8 that was standard with the model and is fitted with a four-speed manual transmission.